What is Powder Coating Powder Manufacturing Process?
Powder coating is one of the most preferred surface finishing methods for the high-quality diecasting's that MRT produces.
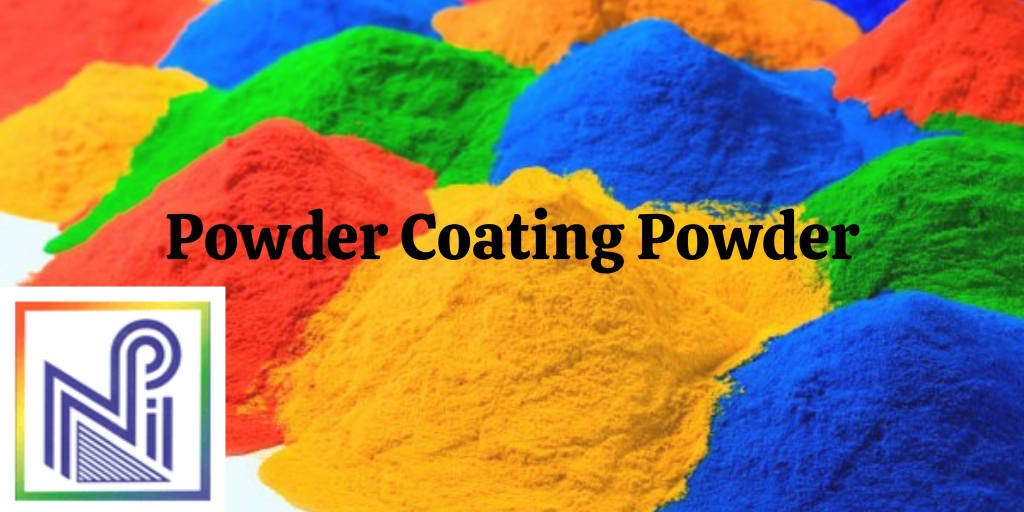
What is powder coating?
Powder coating is one of the most preferred surface finishing methods for the high-quality diecasting's that MRT produces. Spraying color dry powder, a blend of pigment and resin, from a highly controllable gun onto the desired surface is the procedure. Because the powder and the part to be coated are electrostatically charged in opposite directions, they are attracted to one other. This charge causes the powder to adhere to the surface in a thicker, more even coating than most standard paint applications. Because of the nature of the powder coating process and application, the coating is applied evenly and into all of the difficult-to-reach regions.
Powder coating is a method of coloring metals such as steel and aluminum that is more often preferred over painting because it provides a longer-lasting, more durable finish. The most important thing to know about powder coating is that it can produce practically any color. Solid bright, deep neutrals, and fading and blending color combinations on the same structure are all feasible. Powder coating works just as well with one-offs and small batches as it does with large manufacturing, so we've seen designers provide a number of color options on powder coated products on a regular basis.
Manufacture of powder coating
Raw material pre-mixing - When all of the raw elements used in powder coatings are combined together, they form a solid. In a mixing vessel, the polymer and additional materials like as color's, fillers, and cross linkers are precisely weighed. After that, the materials are combined together to make a homogenous mixture.
Extrusion - The pre-mixture is then put into the extruder, which has a barrel that is kept at a precise temperature. The temperature in the barrel is set to just liquefy the polymer. A high temperature causes low melt viscosity, low shear, and poor pigment dispersion, resulting in coatings that do not perform as expected. The speed of the extruder screw and the feed rate on the hopper are then balanced to keep the screw fully loaded. High shear and, as a result, intimate mixing conditions are maintained within the extruder by carefully adjusting these three parameters.
Milling or grinding - After that, the chips are ground to obtain a particle size distribution that is suitable for the application procedure, such as electrostatic spraying or fluid bed dipping. A pin-disc or hammer mill is used for this. An internal classifier is employed in modern mills to control the maximum particle size, with large particles being fed back into the mill on a continuous basis.
POWDER COATING PROCESS
After you've decided on the sort of coating and the materials you'll use to powder coat your product, the powder coating procedure may begin.
CLEAN THE ITEM
- To guarantee a uniform coating, the first stage in the powder coating application process is to clean and completely dry the item.
- Alkaline cleaning is the most popular procedure for working with metal objects.
- The majority of the job is done by professionals using alkaline cleaning tanks.
- Cleaning the metal removes any debris, dust, oils, and residues that could obstruct the powder coating process by preventing the material from adhering to the surface or affecting the finish.
- One thing that must be watched and maintained when preparing and doing alkaline cleaning is the pH of the bath.
- A pH of more than 7 indicates an alkaline liquid; bleach is a frequent household example of an alkaline liquid.
- There are a variety of materials that can fall off an object and end up in the bath. To avoid accumulation, these must be removed throughout the operation.
Overview of Process and Equipment
To neutralize the surface, the part is dipped in a chemical solution. Because each chemical solution is formulated to operate with a specific base material, results will vary. It's either a chromate or phosphate solution on aluminum. Zinc and iron phosphates are two other choices. These chemicals cling to the part's surface and provide the necessary layer for the powder to attach. Last but not least, the item is demineralized to eliminate any chemical salts from the surface and to avoid corrosion beneath the powder coating.
Want to learn more about Powder Coating? Get in touch with the Nivera Paints.
Related Searches
powder coating powder brands in India
powder coating powder manufacturers in India
powder coating powder suppliers near me
powder coating powder suppliers in Delhi
powder coating powder manufacturing process
powder coating powder manufacturers
list of powder coating manufacturers in India
powder coating paint price in India
About the Creator
Maddy Singh
I'm Maddy Singh, a passionate digital marketing executive and blogger. I take great pride in my work and maintain a positive attitude towards it. It brings me joy to contribute and deliver valuable insights to readers through my blog.
Comments
There are no comments for this story
Be the first to respond and start the conversation.