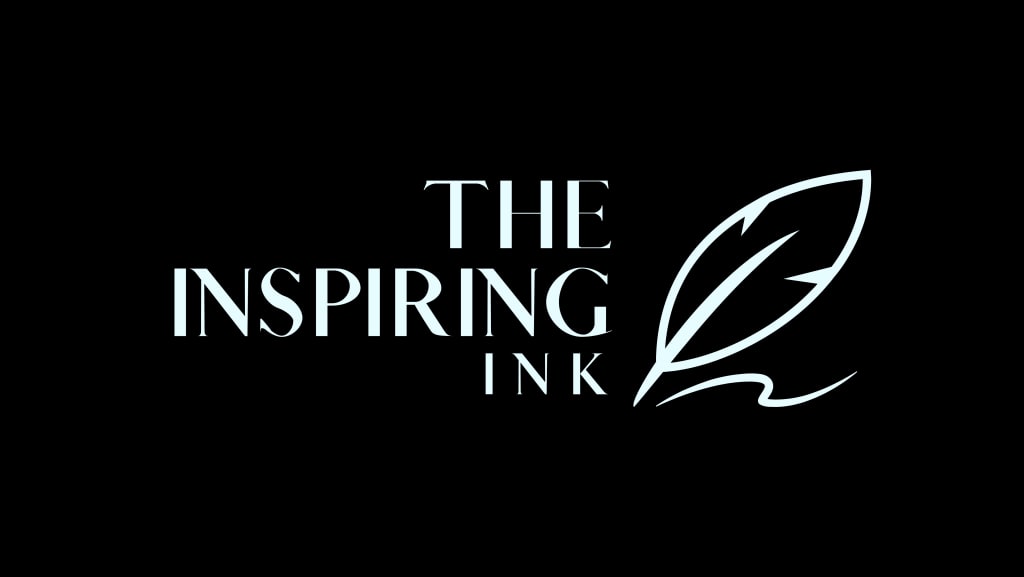
and technical repairs. The operators are responsible for upkeep of their equipment to prevent it
from deteriorating.
Steps in JISHU HOZEN
1. Train the employees: Educate the employees about TPM, its advantages, JH advantages
and steps in JH. Educate the employees about abnormalities in equipments.
2. Initial cleanup of machines
Supervisor and technician should discuss and set a date for implementing step 1.
Arrange all items needed for cleaning.
On the arranged date, employees should clean the equipment completely with the
help of maintenance department.
Dust, stains, oils and grease has to be removed.
Following are the things that have to be taken care while cleaning. They are oil
leakage, loose wires, unfastened nits and bolts and worn out parts.
After clean up problems are categorized and suitably tagged. White tags are place
where operators can solve problems. Pink tag is placed where the aid of maintenance
department is needed.
Contents of tag are transferred to a register.
Make note of area, which were inaccessible.
Finally close the open parts of the machine and run the machine.
3. Counter measures
Inaccessible regions had to be reached easily, e.g., if there are many screw to open
a flywheel door, hinge door can be used. Instead of opening a door for inspecting
the machine, acrylic sheets can be used.
To prevent work out of machine parts necessary action must be taken.
Machine parts should be modified to prevent accumulation of dirt and dust.
4. Tentative standard
JH schedule has to be made and followed strictly.
Schedule should be made regarding cleaning, inspection and lubrication and it also
should include details like when, what and how.
5. General inspection
The employees are trained in disciplines like pneumatics, electrical, hydraulics,
lubricant and coolant, drives, bolts, nuts and safety.
This is necessary to improve the technical skills of employees and to use inspection
manuals correctly.
After acquiring this new knowledge the employees should share this with others.
By acquiring this new technical knowledge, the operators are now well aware o
6. Autonomous inspection
New methods of cleaning and lubricating are used.
Each employee prepares his own autonomous chart/schedule in consultation with
supervisor.
Parts which have never given any problem or part which don’t need any inspection
are removed from list permanently based on experience.
Including good quality machine parts. This avoid defects due to poor JH.
• Inspection that is made in preventive maintenance is included in JH.
The frequency of cleanup and inspection is reduced based on experience.
7. Standardization
Up to the previous stem only the machinery/equipment was the concentration.
However, in this step the surroundings of machinery are organized. Necessary
items should be organized, such that there is no searching and searching time is
reduced.
Work environment is modified such that there is no difficulty in getting any item.
Everybody should follow the work instructions strictly.
Necessary spares for equipments is planned and procured.
8. Autonomous management
OEE and OPE and other TPM targets must be achieved by continuous improve
through Kaizen.
PDCA (Plan, Do, Check and Act) cycle must be implemented for Kaizen.
PILLAR 3—KAIZEN
‘Kai’ means change, and ‘Zen’ means good (for the better). Basically Kaizen is for small
improvements, but carried out on a continual basis and involve all people in the organization.
Kaizen is opposite to big spectacular innovations. Kaizen requires no or little investment. The
principle behind is that “a very large number of small improvements are more effective in an
organizational environment than a few improvements of large value.” This pillar is aimed at
reducing losses in the workplace that affect our efficiencies. By using a detailed and thorough
procedure we eliminate losses in a systematic method using various Kaizen tools. These activities
are not limited to production areas and can be implemented in administrative areas as well.
Kaizen Policy
1. Practice concepts of zero losses in every sphere of activity.
2. Relentless pursuit to achieve cost reduction targets in all resources.
3. Relentless pursuit to improve overall plant equipment effectiveness.
4. Extensive use of PM analysis as a tool for eliminating losses.
5. Focus of easy handling of operators.
Kaizen Target
Achieve and sustain zero loses with respect to minor stops, measurement and adjustments
About the Creator
The Inspiring Ink
Welcome to my blog!
Here, I share my thoughts and insights on a variety of topics including technology, business and personal development. Join us on the journey of discovery and growth and share your own thoughts in the comments section.
Comments
There are no comments for this story
Be the first to respond and start the conversation.