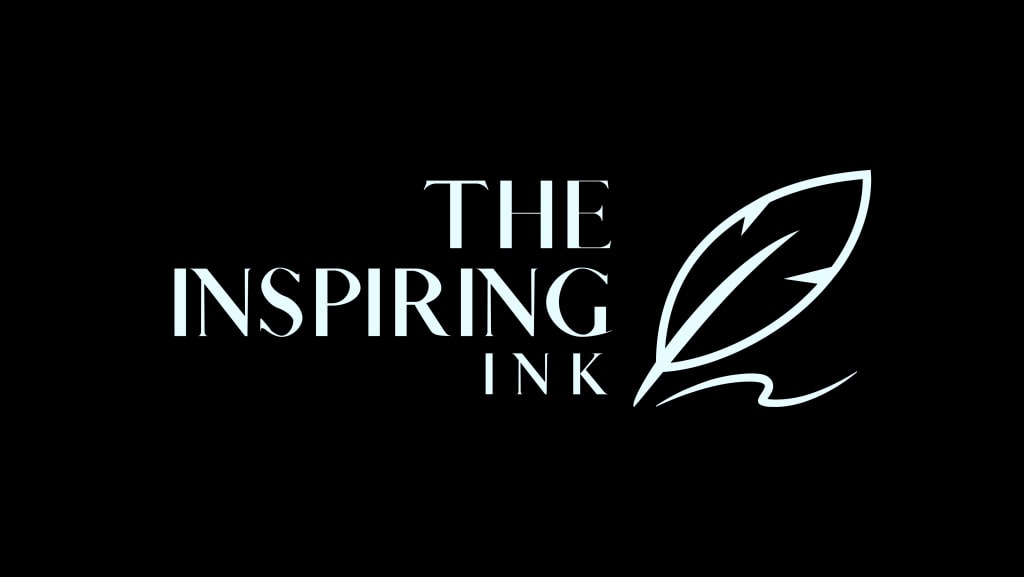
C. EVALUATION AND SELECTION OF THE SUPPLIER
The purchase policy and procedure differ according to the type of items to be purchased. Hence,
evolution and selection of the supplier differ accordingly. In the ‘purchasing handbook’ edited by
Aljian, it has been described that the following variables to be considered while evaluating the
quotations of the suppliers:
1. Cost Factors
Price, transportation cost, installation cost if any, tooling and other operations cost, incidence of
sales tax and excise duty, terms of payment and cash discount are considered in cost factor.
2. Delivery
Routing and F.O.B. terms are important in determining the point at which the title to the goods
passes from vendor to the buyer and the responsibility for the payment of the payment charges.
3. Design and Specification Factors
Specification compliance, specification deviations, specification advantages, important dimensions
and weights are considered in line with the demonstration of sample, experience of other users,
after sale services etc.
4. Legal Factors
Legal factors include warranty, cancellation provision, patent protection, public liability, federal
laws and reputation compliance.
5. Vendor Rating
The evaluation of supplier or vendor rating provides valuable information which help in improving
the quality of the decision. In the vendor rating three basic aspects are considered namely quality,
service and price. How much weight should be given to each of these factors is a matter of
judgment and is decided according to the specific need of the organization. Quality would be the
main consideration in the manufacturing of the electrical equipments while price would be the
prime consideration in the product having a tense competitive market and for a company procuring
its requirements under the blanket contract with agreed price, the supplier rating would be done
on the basis of two variables namely quality and delivery.
The Development Project Committee of the National Association of Purchasing Agents
(U.S.A.) has suggested following methods for evaluating the performance of past suppliers.
1. The categorical plan: Under this method the members of the buying staff related with
the supplier like receiving section, quality control department, manufacturing department etc., are
required to assess the performance of each supplier. The rating sheets are provided with the record
of the supplier, their product and the list of factors for the evaluation purposes. The members of
the buying staff are required to assign the plus or minus notations against each factor. The periodic
meetings, usually at the interval of one month, are held by senior man of the buying staff to consider
the individual rating of each section. The consolidation of the individual rating is done on the basis
of the net plus value and accordingly, the suppliers are assigned the categories such as ‘preferred’,
‘neutral’ or ‘unsatisfactory’. Such ratings are used for the future guidance.
The evaluation of each supplier is made in accordance with the aforesaid factors and
weights and the composite weighted-points are ascertained for each suppliers—A, B and C—
are rated under this method. First of all the specific rating under each factor will be made and
then the consolidation of all the factors will be made for the purpose of judgment.
Quality rating: Percentage of quantity accepted among the total quantity is called quality
rating. In other words, the quality of the materials is judged on the basis of the degree of
acceptance and rejections. For the purpose of comparison, the percentage degree of acceptance
will be calculated in relation to the total lots received. Price rating is done on the basis of net
price charged by the supplier. Timely delivery rating will be done comparing with the average
delivery schedule of the supplier.
3. The cost-ratio plan: Under this method, the vendor rating is done on the basis of various
costs incurred for procuring the materials from various suppliers. The cost-ratios are ascertained
delivery etc. The cost-ratios are ascertained for the different rating variables such as quality,
price, timely delivery etc. The cost-ratio is calculated in percentage on the basis of total individual
cost and total value of purchases. At the end, all such cost-ratios will be adjusted with the quoted
price per unit. The plus cost-ratio will increase the unit price while the minus cost-ratio will
decrease the unit price. The net adjusted unit price will indicate the vendor rating. The vendor
with the lowest net adjusted unit price will be the best supplier and so on. Certain quality costs
can be inspection cost, cost of defectives, reworking costs and manufacturing losses on rejected
items etc. Certain delivery costs can be postage and telegrams, telephones and extra cost for
quick delivery etc.
About the Creator
The Inspiring Ink
Welcome to my blog!
Here, I share my thoughts and insights on a variety of topics including technology, business and personal development. Join us on the journey of discovery and growth and share your own thoughts in the comments section.
Comments
There are no comments for this story
Be the first to respond and start the conversation.