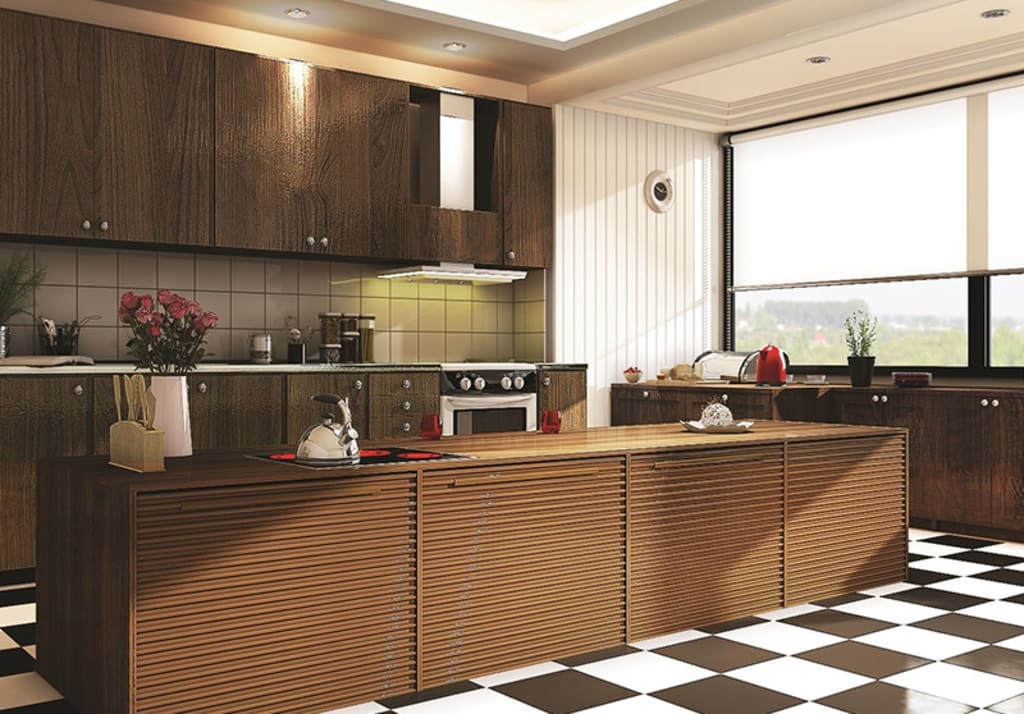
We all know that a plywood sheet is composed of at least three thin coatings of wood glued together. Every sheet of wood, or handle, is usually placed with its grain running at the correct points to the surrounding substrate, with the intention of reducing the shrinkage and enhancing the consistency of the finished piece. The bulk of compressed wood is pressed into large, level sheets used for building development. Other pressed bits of wood can be framed in simple or complicated bends for use in furniture, warships, and aircraft. Let's have a deep dive.
The use of thin sheets of laminated MDF as a means of development dates back to about 1500 B.C. At the point where the Egyptian experts joined the thin pieces of dull dark wood to the outer wooden coffin found in the tomb of King Tut-Ankh-Amon. This method was later used by the Greeks and Romans to make fine furniture and other fancy items. In the 1600s, the craft of finishing furniture with thin sections of wood ended up becoming known as veneering, and the pieces themselves wound up becoming known as a painting.
In 1928, the main standard sheets, 4 feet by 8 feet (1.2 m by 2.4 m), were proposed for use as construction material. In the coming decades, improved cement and modern manufacturing methods have made it possible for compressed wood to be used for a wide variety of applications. Today, waterproof plywood has sold cut timber for certain developmental reasons, and compressed wood production has become a multi-billion dollar business as a whole.
1) Marine Plywood.
Marine plywood is of higher quality than standard water resistant plywood and is therefore considerably more costly. It is not usually used for indoor purposes, such as having a table, chair or bed. It is somewhat used for applications such as the construction of vessels and other modern purposes, where plywood would certainly inspire a bland display of water.
2) Flexible Plywood
This flexible plywood sheet is regularly referred to as 'bendy plywood' or 'flex use' and is used in furniture and shop fittings anywhere the bends are desirable, along these lines requiring a board that is highly adaptable. Flexible plywood with this adaptable trademark is made from an uncommonly treated facade, usually with a thinner focal core veneer and two thicker 'kneaded' external facades.
3) Aircraft plywood
This form of plywood comes with high strength, and is also known as aircraft plywood. High-strength plywood, also known as aircraft plywood, is made from mahogany. It was used in the design of air attack aircraft during the Second World War, as well as other fighter aircraft. Nicknamed "The Wooden Wonder" plywood was used for wing surfaces, as well as for flat areas such as bulkheads and wing sparse webs. The fuselage had extraordinary stiffness due to the bonded ply-balsa-ply 'sandwich' of its monologic shell; the elliptical cross-section was shaped in two distinct mirror-image halves, using curved molds.
4) Tropical plywood
Tropical plywood is made continuously from mixed tropical wood types. Tropical plywood boasts its prevalence over softwood due to its width, consistency, uniformity of layers and high calibre. It is usually sold, with any built-in prices, in a variety of market sectors whenever it is assembled in compliance with exclusive specifications. Tropical compressed wood is essentially known for its durability and consistency, which is commonly used by Asian nations. The reality of tropical plywood offered by various plywood dealers is lightweight and heavy, but not consistently moderate, tropical pressed wood is mainly used in the small-scale industry.
5) Hardwood Plywood
Hardwood pressed wood is known for its high quality, solidity and protection from creeping. Hardwood compressed wood is suitable for a variety of standard applications. Typically used in cabinets and furniture making. Numerous melodic instruments are constructed from hardwood compressed wood, like pianos and string instruments. It has irregular state quality and affect and resistance, which render it especially ideal for uncompromising flooring and partitioning systems. Hardwood plywood has superior hardness on the board.
6) Softwood Plywood
Softwoods, for the most part, are made from a gymnosperm tree. This makes it possible for the seeds to disperse and grow over a wide area. In addition, this is the motivation behind which most softwood trees can develop; in general, it grows in giant tracts that can spread across miles like 'oak' and timberlands. Much softwood will usually come from conifers such as pines, pines and spruces. Any of the well-known softwood trees are oak, redwood, fir, cedar and larch. Softwood is fairly mainstream and natural. It is, to say the truth, the cause of about 80% of the world's timber supply.
7) Veneer
The veneer features a thin cut of wood, usually more fine than 3mm, which is regularly stuck on centre boards to make level boards, e.g. doorways, tops and boards for cupboards and part of furniture.
There are few forms of veneer available on the market, such as:
· Raw veneer has no protection and can be used on any hand facing up. Notice that the opposite sides can look distinctive when the whole is associated, owing to the cellular arrangement of the wood.
· A paper-backed veneer is, as the name implies, a veneer that is supported by paper. The alternative view is that it is available in large quantities or boards, as small parts are consolidated prior to, including the support. This is beneficial for clients who do not want to enter little fragments of raw veneer.
· Laid up veneer is a simple veneer that has been mixed to create large bits. This operation takes too long and requires a lot of alertness. The veneer can be bought from a company that, as of now, has every scale, form, and shape.
8) Exterior Plywood.
The exterior plywood has an environment and water-safe paste that connects each veneer. When you make laminated MDF outdoors, one of the biggest – and most vital – issues is how wood can cope with wind, fog, and other climates. Exterior wood is designed to combat the components to have a sturdy, powerful casing for a substantial period of time to come.
9) Lumber Core Plywood
Lumber Core Plywood is usually composed of three layers, with two thin veneers on each side and a dense core. The outer veneer is typically made of hardwood, while the inner one of the cores is made of bits of wood trapped in one solid section.
The internal core helps to get a grip on the screws, which allows a good decision for tasks involving a strong screw hold. One downside is that sloppy lumber centre plywood can have holes within the centre that limit the quality of the water resistant plywood and the holding power of the screw.
About the Creator
Amit Kr
Hi I am Amit Kr from India. I love writing on various topics. I love nature, music, pets and weekend traveling.
Comments
There are no comments for this story
Be the first to respond and start the conversation.