Servo Motors: Repair or Replace?
Do You Have a Broken Servo Motor Repair or Replace Policy?
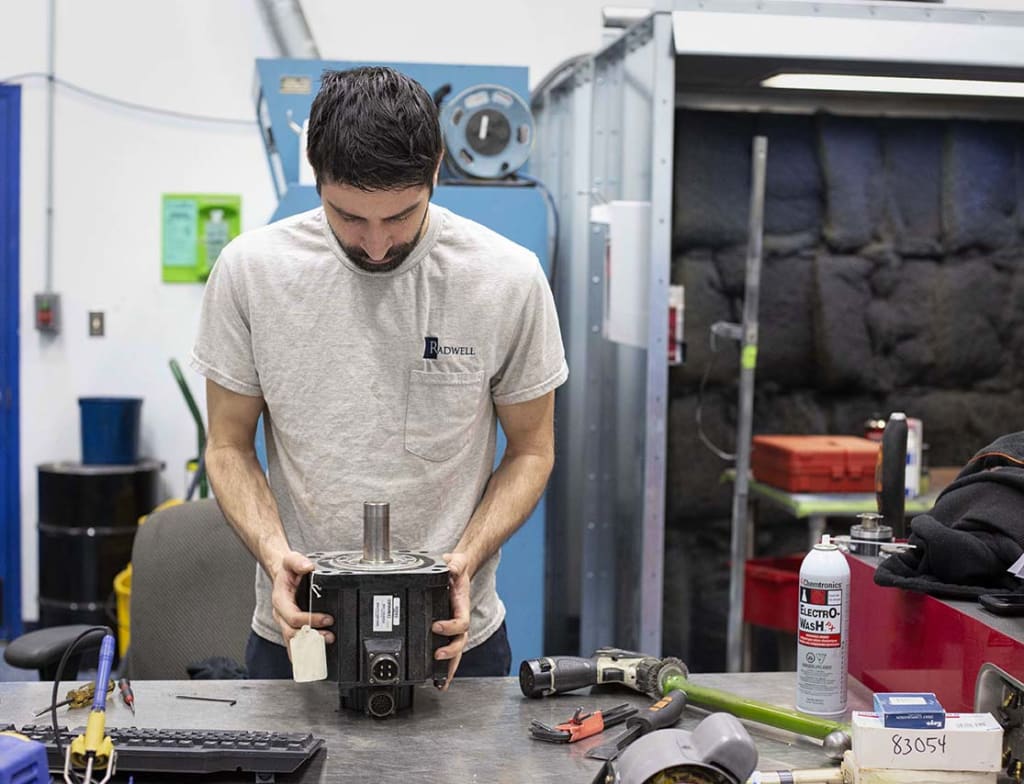
If you manage an industrial automation process, you rely on equipment to help you maintain maximum efficiency. You’ll want to employ a careful engineering approach so you can continue to serve your clients, whether they’re involved in manufacturing or are part of a supply chain. Breakdowns are to be avoided at all costs, but when they do happen, should you conduct something like a servo motor repair or replace it? Radwell International Ltd can help you with complicated automation decisions like that, but what do you need to bear in mind in the meantime?
Cost Versus Time
Sooner or later, you will face a critical conundrum. Should you repair or replace a motor, and what factors do you need to take into consideration?
Essentially, your answer will depend on two major variables – cost and time. You will be losing money by the minute if the motor failure has caused your production line to stop, and you will want to ensure that the machinery is replaced as quickly as possible. On the other hand, you may have time to spare, so if you can maintain productivity and if time is not critical, it may be better for you to repair it instead.
Why Are Motors So Important?
Servo motors are in widespread use throughout industry and for a good reason. They are highly reliable, relatively small and fairly quiet. They can produce high output levels in relation to their size and are very well suited if the environment is demanding or vibration levels may be high.
Where to Start
To begin with, determine the age of the part and whether a new design or enhanced technology is available. Would a complete replacement be more appropriate if it brings advantages to your process? This type of replacement could be more reliable in the future as well.
Remember that older motors may not be as efficient, and this may be the opportunity for you to reduce some of your energy costs. This could help you bring down the size of your carbon footprint, and you could enjoy some reputational benefits down the road.
It is also important to think about rewinding. Many motors can be rewound a number of times during their life, and this will sometimes make them even more efficient than they were before. If you give the task to an experienced technician, they will likely do a superior job by hand, as compared to the original machine-installed work.
If the design and tech are fairly recent, determine the severity of the damage. It may be more costly to repair the item if the damage is to the core or the rotor, for example.
In any case, you should develop a motor failure replacement and repair policy based on your specific needs, configuration, budget and goals. When you do, you’ll be able to make crucial decisions quickly and without the need for procrastination. If need be, you can get the materials or equipment needed ready in advance to be even better prepared.
Crafting Your Policy
What do you need to consider as you design your policy?
Begin by gathering information and working out ways to record run hours and previous performance. You want to know how much it would cost to replace the motor while taking into account any discounts you might get from your repair shop. You will also want to know how much it costs you to run the particular motor in terms of energy use.
Repair or Replace
You need to be quite granular here and use real-time costs wherever possible. Are you comparing like-for-like when figuring out those equations? Remember, you can expect a new motor to last a lot longer than one that needs repair, so should take this into account when comparing purchase cost versus repair cost.
As you calculate, you will be able to come up with a figure that shows you whether it would be cost-effective to repair a motor based on expected payback. You can generate a trigger point, beneath which you should always repair and above which you should replace.
Remember, energy costs represent most of the life cycle expenditure, so you’ll always need to be looking for efficiency.
Failure Analysis
You will also need to implement a review policy to determine why an individual motor may be failing more often than it should.
Do you have the right type of motor fitted for the task in question? To gather the appropriate detail, you may have to ask your repair shop to give you some feedback. They can perform a root cause failure analysis, and this may shed some light on the issue. You may find that you are using motors that are not built for the type of environment and may need to upgrade them. You may have an issue with power supply, and a surge problem may cause damage from time to time.
Conversely, you may be wasting money if you have a heavy-duty motor operating in a position with low load requirement. Once you identify this situation, you can replace those units with a more appropriate model, and this will not only help with efficiency but reduce your overall energy spend as well.
Establishing a Repair Partner
You will want to identify your repair partner in this document so that equipment is always sent to your preferred vendor. Make sure that you talk with the service centre first and let them know what’s happening and ensure that they can always provide you with the required feedback. Remember, they may be called upon to perform a root cause analysis to provide you with valuable information.
Partner Criteria
You must ensure that your chosen partner can repair in accordance with best industry practice and can provide you with the appropriate warranty where needed. They should only use equipment that has been calibrated properly and measured accurately, so you know that any repairs will be satisfactory.
Is your partner well placed to provide you with a range of additional tests? Can they test insulation resistance, for example, or make surge comparisons? They will need to confirm that their internal systems and power supplies are sufficient to enable them to conduct the various tests along the way.
Furthermore, does the repair partner have access to spares whenever needed, and can they ensure that their own supply chain is up to the task? If so, they’ll be able to guarantee turnaround times for repair, as they will always have the requisite parts on hand.
Communication
Finally, once you have compiled your motor failure policy, ensure that it is communicated to all concerned. Everyone involved in operating or maintaining the equipment must know what to do and when to do it. Then, you need to place ID tags on each motor to tell whoever is on duty at a moment of crisis what to do. They’ll know whether to repair or replace the motor and how to get in touch with the nominated repair shop.
In Summary
Martin Thomas, European Marketing Manager at Radwell said “Productivity is key, and you will want to avoid downtime wherever possible. Yet you also need to know when to repair rather than replace, and this is why you should have an up-to-date policy ready. When you do, you will not only minimize downtime, but you will also eliminate confusion, keep your staff more informed, and ultimately, save money.
Radwell International offers full repair and testing capabilities for servo motors, with a dedicated Servo Motor Shop and value-added repair service, so don’t hesitate to reach out for advice.”
About the Creator
Radwell International Ltd
Award-winning global leader in industrial automation solutions.
We buy, sell and repair new, used and obsolete industrial automation parts including PLCs, servo motors, HMIs, drives, PCBs, safety scanners and robotics.
Comments
There are no comments for this story
Be the first to respond and start the conversation.