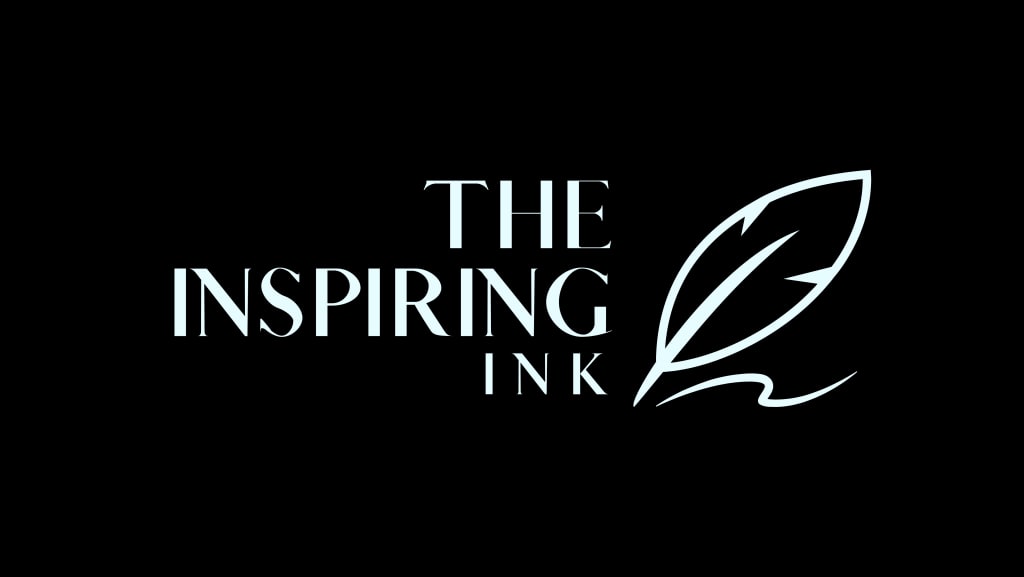
1. THE BUSINESS PLAN
The business plan is a statement of the organization’s overall level of business activity for the
coming six to eighteen months, usually expressed in terms of outputs (in volume of sales) for its
various product groups, a set of individual products that share or consume common blocks of
capacity in the manufacturing process. It also specifies the overall inventory and backlog levels
that will be maintained during the planning period. The business plan is an agreement between
all functional areas—finance, production, marketing, engineering, R & D—about the level of
activity and the products they are committed to support. The business plan is not concerned with
all the details and specific timing of the actions for executing the plan. Instead, it determines a
feasible general posture for competing to achieve its major goals. The resulting plan guides the
lower-level, more details decisions.
2. AGGREGATE PRODUCTION (OUTPUT) PLANNING
The process of determining output levels of product groups over the coming six to eighteen
months on a weekly or monthly basis. It identifies the overall level of outputs in support of the
business plan. The plan recognizes the division’s existing fixed capacity and the company’s
overall policies for maintaining inventories and backlogs, employment stability and subcontracting.
3. AGGREGATE CAPACITY PLANNING
It is the process of testing the feasibility of aggregate output plans and evaluating overall capacity
utilisation. A statement of desired output is useful only if it is feasible. Thus, it addresses the
supply side of the firm’s ability to meet the demand. As for aggregate output plans, each plant,
facility, or division requires its own aggregate capacity plan. Capacity and output must be in
balance, as indicated by the arrow between them in Fig. 5.3. A capacity plan translates an output
plan into input terms, approximating how much of the division’s capacity will be consumed.
Although these basic capacities are fixed, management can manipulate the short-term capacities
by the ways they deploy their work force, by subcontracting, or by using multiple work shifts
to adjust the timing of overall outputs. As a result, the aggregate planning process balances output
levels, capacity constraints, and temporary capacity adjustments to meet demand and utilise
capacity at desired levels during the coming months. The resulting plan sets limits on the master
production schedule.
4. MASTER PRODUCTION SCHEDULING (MPS)
MPS is a schedule showing week by week how many of each product must be produced
according to customer orders and demand forecasts. Its purpose is to meet the demand for
individual products in the product group. This more detailed level of planning disaggregates the
product groups into individual products and indicates when they will be produced. The MPS is
an important link between marketing and production. It shows when incoming sales orders can
be scheduled into production, and when each shipment can be scheduled for delivery. It als
for material requirements planning. MRP provides information such as due dates for components
that are subsequently used for shop floor control. Once this information is available, it enables
managers to estimate the detailed requirements for each work centres.
7. CAPACITY REQUIREMENT PLANNING
Capacity requirement planning (CRP) is an iterative process of modifying the MPS or planned
resources to make capacity consistent with the production schedule. CRP is a companion process
used with MRP to identify in detail the capacity required to execute the material requirement
planning. At this level, more accurate comparisons of available and needed capacity for scheduled
workloads are possible.
8. SHOP FLOOR CONTROL
Shop floor control involves the activities that execute and control shop operations namely loading,
sequencing, detailed scheduling and expediting jobs in production. It coordinates the weekly and
daily activities that get jobs done. Individual jobs are assigned to machines and work centres
(loading), the sequence of processing the jobs for priority control is determined, start times and
job assignments for each stage of processing are decided (detailed scheduling ) and materials and
work flows from station to station are monitored and adjusted (expediting).
9. LOADING
Each job (customer order) may have its unique product specification and, hence, it is unique
through various work centres in the facility. As new job orders are released, they are assigned
or allocated among the work centres, thus establishing how much of a load each work centre
must carry during the coming planning period. This assignment is known as loading (sometimes
called shop loading as machine loading).
10. SEQUENCING
This stage establishes the priorities for jobs in the queues (waiting lines) at the work centres.
Priority sequencing specifies the order in which the waiting jobs are processed; it requires the
adoption of a priority sequencing rule.
11. DETAILED SCHEDULING
Detailed scheduling determines start times, finish times and work assignments for all jobs at each
work centre. Calendar times are specified when job orders, employees, and materials (inputs),
as well as job completion (outputs), should occur at each work centre. By estimating how long
each job will take to complete and when it is due, schedulers can establish start and finish dates
and develop the detailed schedule
About the Creator
The Inspiring Ink
Welcome to my blog!
Here, I share my thoughts and insights on a variety of topics including technology, business and personal development. Join us on the journey of discovery and growth and share your own thoughts in the comments section.
Comments
There are no comments for this story
Be the first to respond and start the conversation.