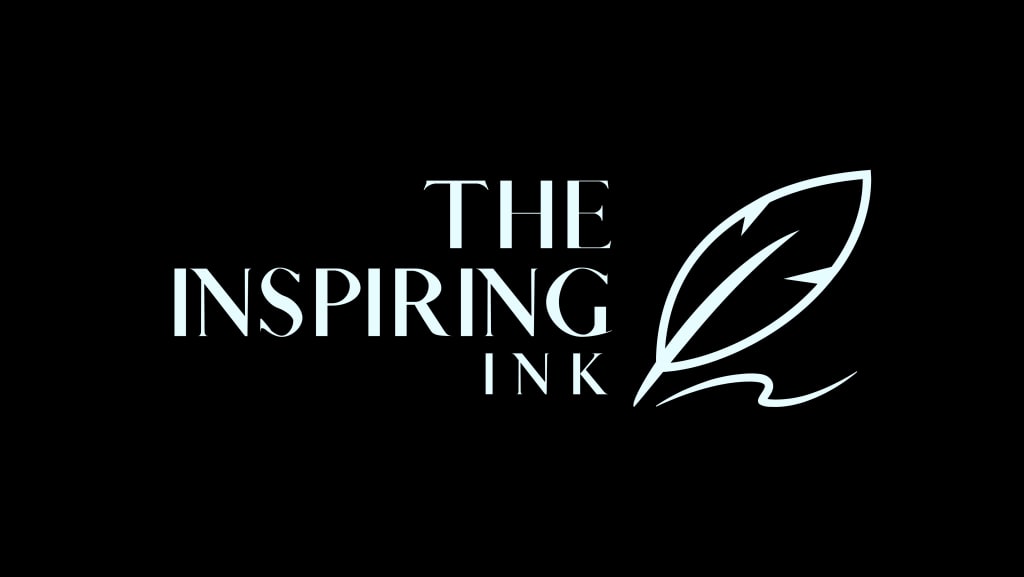
Aggregate planning is an intermediate term planning decision. It is the process of planning the
quantity and timing of output over the intermediate time horizon (3 months to one year). Within
this range, the physical facilities are assumed to –10 be fixed for the planning period. Therefore,
fluctuations in demand must be met by varying labour and inventory schedule. Aggregate planning
seeks the best combination to minimise costs.
Aggregate Planning Strategies
The variables of the production system are labour, materials and capital. More labour effort is
required to generate higher volume of output. Hence, the employment and use of overtime (OT)
are the two relevant variables. Materials help to regulate output. The alternatives available to the
company are inventories, back ordering or subcontracting of items.
These controllable variables constitute pure strategies by which fluctuations in demand and
uncertainties in production activities can be accommodated by using the following steps:
1. Vary the size or the workforce: Output is controlled by hiring or laying off workers in
proportion to changes in demand.
2. Vary the hours worked: Maintain the stable workforce, but permit idle time when there
is a slack and permit overtime (OT) when demand is peak.
3. Vary inventory levels: Demand fluctuations can be met by large amount of inventory.
4. Subcontract: Upward shift in demand from low level. Constant production rates can be
met by using subcontractors to provide extra capacity.
Aggregate Planning Guidelines
The following are the guidelines for aggregate planning:
1. Determine corporate policy regarding controllable variables.
2. Use a good forecast as a basis for planning.
3. Plan in proper units of capacity.
4. Maintain the stable workforce.
5. Maintain needed control over inventories.
6. Maintain flexibility to change.
7. Respond to demand in a controlled manner
Master scheduling follows aggregate planning. It expresses the overall plans in terms of specific
end items or models that can be assigned priorities. It is useful to plan for the material and
capacity requirements.
Flowchart of aggregate plan and master production schedule is shown in Fig. 5.4
Time interval used in master scheduling depends upon the type, volume, and component lead
times of the products being produced. Normally weekly time intervals are used. The time horizon
covered by the master schedule also depends upon product characteristics and lead times. Some
master schedules cover a period as short as few weeks and for some products it is more than a year.
Functions of MPS
Master Production Schedule (MPS) gives a formal details of the production plan and converts
this plan into specific material and capacity requirements. The requirements with respect to
labour, material and equipment is then assessed.
The main functions of MPS are:
1. To translate aggregate plans into specific end items: Aggregate plan determines level
of operations that tentatively balances the market demands with the material, labour and
equipment capabilities of the company. A master schedule translates this plan into specific
number of end items to be produced
in specific time period
Evaluate alternative schedules: Master schedule is prepared by trial and error. Many
computer simulation models are available to evaluate the alternate schedules.
3. Generate material requirement: It forms the basic input for material requirement planning
(MRP).
4. Generate capacity requirements: Capacity requirements are directly derived from MPS.
Master scheduling is thus a prerequisite for capacity planning.
5. Facilitate information processing: By controlling the load on the plant. Master schedule
determines when the delivery should be made. It coordinates with other management
information systems such as, marketing, finance and personnel.
6. Effective utilization of capacity: By specifying end item requirements schedule establishes
the load and utilization requirements for machines and equipment
MRP refers to the basic calculations used to determine components required from end item
requirements. It also refers to a broader information system that uses the dependence relationship
to plan and control manufacturing operations.
“Materials Requirement Planning (MRP) is a technique for determining the quantity
and timing for the acquisition of dependent demand items needed to satisfy master production
schedule requirements.
1. Inventory reduction: MRP determines how many components are required when they
are required in order to meet the master schedule. It helps to procure the materials/ components
as and when needed and thus avoid excessive build up of inventory.
2. Reduction in the manufacturing and delivery lead times: MRP identifies materials
and component quantities, timings when they are needed, availabilities and procurements and
actions required to meet delivery deadlines. MRP helps to avoid delays in production and priorities
production activities by putting due dates on customer job order.
3. Realistic delivery commitments: By using MRP, production can give marketing timely
information about likely delivery times to prospective customers.
4. Increased efficiency: MRP provides a close coordination among various work centres
and hence help to achieve uninterrupted flow of materials through the production line. This
increases the efficiency of production system
About the Creator
The Inspiring Ink
Welcome to my blog!
Here, I share my thoughts and insights on a variety of topics including technology, business and personal development. Join us on the journey of discovery and growth and share your own thoughts in the comments section.
Comments
There are no comments for this story
Be the first to respond and start the conversation.