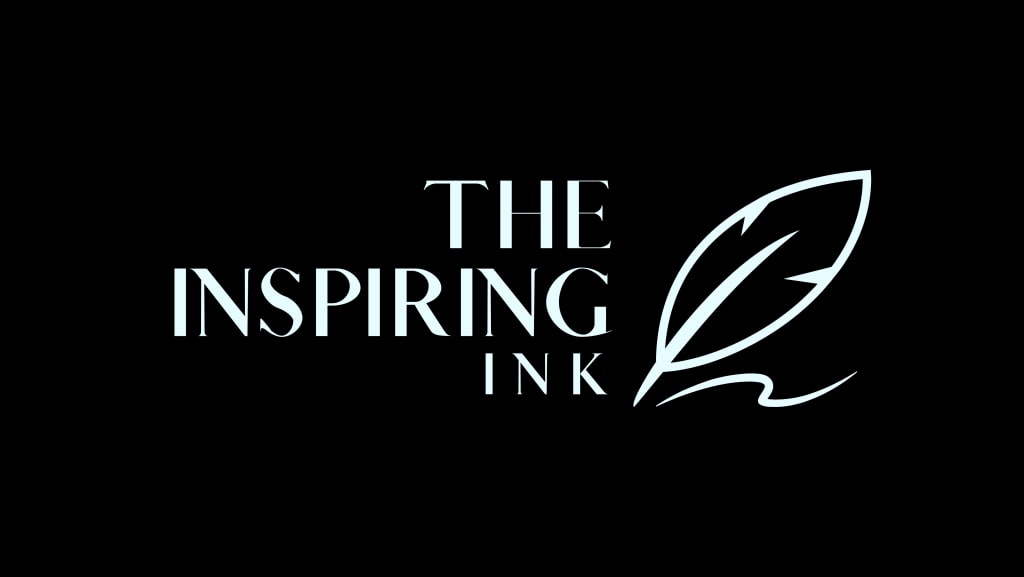
Characteristics of Robot Applications. The general characteristics of industrial
work situations that tend to promote the substitution of robots for human labor are the
following:
1. Hazardous work for humans. When the work and the environment in which it is performed are hazardous, unsafe, unhealthful, uncomfortable, or otherwise unpleasant
for humans, an industrial robot should be considered for the task. In addition to die
casting, there are many other work situations that are hazardous or unpleasant for
humans, including spray painting, arc welding, and spot welding. Industrial robots
are applied in all of these processes.
2. Repetitive work cycle. A second characteristic that tends to promote the use of robotics is a repetitive work cycle. If the sequence of motion elements in the work
cycle is the same, or nearly the same, a robot is usually capable of performing the
cycle with greater consistency and repeatability than a human worker. Greater consistency and repeatability are manifested as higher product quality than what can be
achieved in a manual operation.
3. Difficult handling for humans. If the task involves the handling of parts or tools that
are heavy or otherwise difficult to manipulate, an industrial robot may be available
that can perform the operation. Parts or tools that are too heavy for humans to
handle conveniently are well within the load-carrying capacity of a large robot.
4. Multishift operation. In manual operations requiring second and third shifts, substitution of a robot provides a much faster financial payback than a single shift operation. Instead of replacing one worker, the robot replaces two or three workers.
5. Infrequent changeovers. Most batch or job shop operations require a changeover of
the physical workplace between one job and the next. The time required to make the
changeover is nonproductive time because parts are not being made. Consequently,
robots have traditionally been easier to justify for relatively long production runs
where changeovers are infrequent. Advances have been made in robot technology to reduce programming time, and shorter production runs have become more
economical.
6. Part position and orientation are established in the work cell. Most robots in today’s
industrial applications do not possess vision capability. Their capacity to pick up a
part or manipulate a tool during each work cycle relies on the work unit being in a
known position and orientation. The work unit must be presented to the robot at
the same location each cycle.
As indicated in Section 8.4.1, material handling applications include (1) material
transfer, in which case Equation (8.1) reduces to Tc = Th, or (2) machine loading and/or
unloading, in which the robot is used to support a principal production machine performing the actual processing operation. In the second case, the robot’s participation in the
work cycle is Th, and the production machine consists of To and possibly Tt, depending on
the type of process.
If the robot application consists of a processing operation, in which the robot manipulates some tool as its end effector, then the robot is the principal production machine,
and Equation (8.1) is probably a representative model for the work cycle. Work part
handling is performed by support equipment, perhaps another robot or a human worker
as a last resort.
The production rate of a robotic cell is based on the average production time, which
must include the time to set up the cell.
To accomplish useful work, a robot must be programmed to perform a motion cycle.
A robot program can be defined as a path in space to be followed by the manipulator,
combined with peripheral actions that support the work cycle. Examples of peripheral
actions include opening and closing a gripper, performing logical decision making, and
communicating with other pieces of equipment in the cell. A robot is programmed by
entering the programming commands into its controller memory. Different robots use
different methods of entering the commands.
In the case of limited-sequence robots, programming is accomplished by setting limit
switches and mechanical stops to control the endpoints of its motions. The sequence in
which the motions occur is regulated by a sequencing device. This device determines the
order in which each joint is actuated to form the complete motion cycle. Setting the stops
and switches and wiring the sequencer is more akin to a manual setup than programming.
Today, nearly all industrial robots have digital computers as their controllers, and
compatible storage devices as their memory units. For these robots, three programming
methods can be distinguished: (1) leadthrough programming, (2) computer-like robot
programming languages, and (3) off-line programming
About the Creator
The Inspiring Ink
Welcome to my blog!
Here, I share my thoughts and insights on a variety of topics including technology, business and personal development. Join us on the journey of discovery and growth and share your own thoughts in the comments section.
Comments
There are no comments for this story
Be the first to respond and start the conversation.