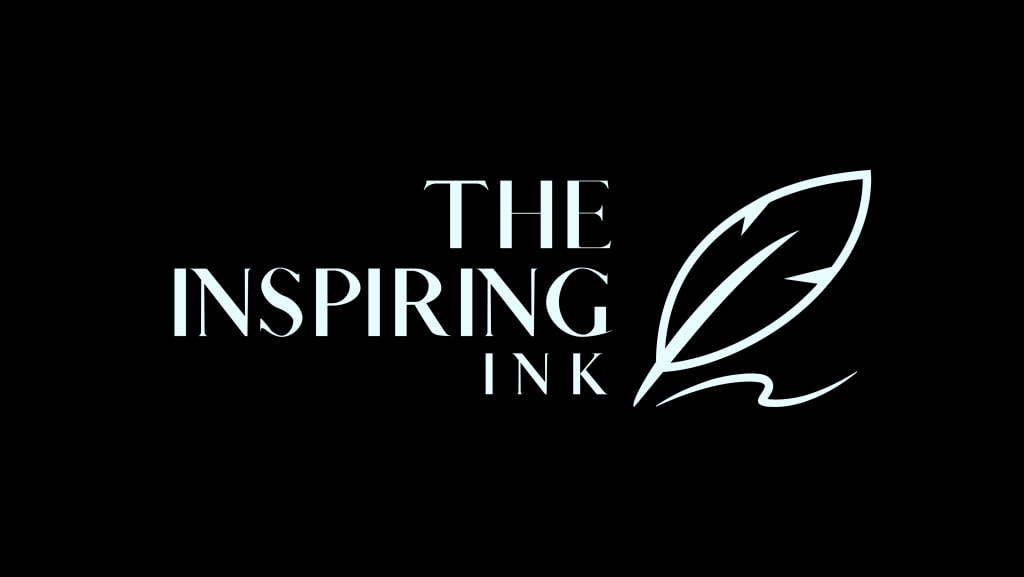
Arc Welding. Arc welding is used to provide continuous welds rather than individual spot welds at specific contact points. The resulting arc-welded joint is substantially
stronger than in spot welding. Because the weld is continuous, it can be used in airtight
pressure vessels and other weldments in which strength and continuity are required. There
are various forms of arc welding, but they all follow the general description given here.
The working conditions for humans who perform arc welding are not good. The
welder must wear a face helmet for eye protection against the ultraviolet light emitted by
the arc welding process. The helmet window must be dark enough to mask the UV radiation. High electrical current is used in the welding process, and this creates a hazard for
the welder. Finally, there is the obvious danger from the high temperatures in the process,
high enough to melt the steel, aluminum, or other metal that is being welded. Significant
hand–eye coordination is required by human welders to make sure that the arc follows
the desired path with sufficient accuracy to make a good weld. This, together with the
conditions described above, results in worker fatigue. Consequently, the welder is only
accomplishing the welding process for perhaps 20–30% of the time. This arc-on time is
defined as the proportion of time during the shift when the welding arc is on and performing the process. To assist the welder, a second worker is usually present at the work site,
called a fitter, whose job is to set up the parts to be welded and to perform other similar
chores in support of the welder.
Because of these conditions in manual arc welding, automation is used where technically and economically feasible. For welding jobs involving long continuous joints that
are accomplished repetitively, mechanized welding machines have been designed to perform the process. These machines are used for long straight sections and regular round
parts, such as pressure vessels, tanks, and pipes.
Industrial robots can also be used to automate the arc welding process. The cell consists of the robot, the welding apparatus (power unit, controller, welding tool, and wire
feed mechanism), and a fixture that positions the components for the robot. The fixture
might be mechanized with one or two axes so that it can present different portions of the
work to the robot for welding (the term positioner is used for this type of fixture). For
greater productivity, two fixtures are often used so that a human helper or another robot
can unload the completed job and load the components for the next work cycle while the
welding robot is simultaneously welding the present job. Figure 8.12 illustrates this kind
of workplace arrangement.
The robot used in arc welding must be capable of continuous path control. Jointedarm robots consisting of six joints are frequently used. Some robot vendors provide manipulators that have hollow upper arms, so that the cables connected to the welding torch
can be contained in the arm for protection, rather than attached to the exterior. Also,
programming improvements for arc welding based on CAD/CAM have made it much
easier and faster to implement a robot welding cell. The weld path can be developed directly from the CAD model of the assembly [9].
Spray Coating. Spray coating directs a spray gun at the object to be coated. Fluid
(e.g., paint) flows through the nozzle of the spray gun to be dispersed and applied over
the surface of the object. Spray painting is the most common application in the category,
but spray coating refers to a broader range of applications that includes painting.
The work environment for humans who perform this process is filled with health
hazards. These hazards include harmful and noxious fumes in the air and noise from the
spray gun nozzle. To mitigate these hazards, robots are being used more and more for
spray coating tasks, particularly in high-production operations.
Robot applications include spray coating of automobile car bodies, appliances,
engines, and other parts; spray staining of wood products; and spraying of porcelain
coatings on bathroom fixtures. The robot must be capable of continuous path control to
accomplish the smooth motion sequences required in spray painting. The most convenient programming method is manual leadthrough (Section 8.5.1). Jointed-arm robots
seem to be the most common anatomy for this application. The robot must possess a
work volume sufficient to access all areas of the work part to be coated in the application.
The use of industrial robots for spray coating offers a number of benefits in addition to protecting workers from a hazardous environment. These other benefits include
greater uniformity in applying the coating than humans can accomplish, reduced waste of
paint, lower needs for ventilating the work area because humans are not present during
the process, and greater productivity.
Other Processing Applications. Spot welding, arc welding, and spray coating are
common processing applications of industrial robots. The list of industrial processes that
are being performed by robots is continually growing. Among these are the following:
• Drilling, routing, and other machining processes. These applications use a rotating
spindle as the end effector. The cutting tool is mounted in the spindle chuck. One of
the problems with this application is the high cutting forces encountered in machining.
The robot must be strong enough to withstand these cutting forces and maintain the
required accuracy of the cut.
About the Creator
The Inspiring Ink
Welcome to my blog!
Here, I share my thoughts and insights on a variety of topics including technology, business and personal development. Join us on the journey of discovery and growth and share your own thoughts in the comments section.
Comments
There are no comments for this story
Be the first to respond and start the conversation.