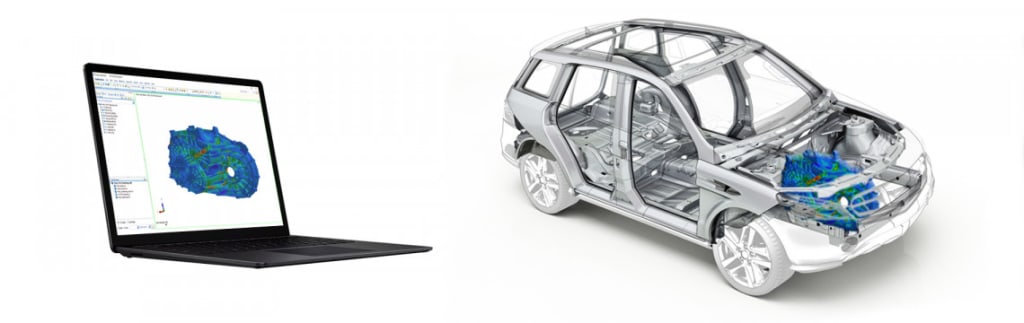
What are the simulation software in modeling metal casting?
It is best to simulate the complete casting process for flawless parts with a single tool each time. By doing this, the first parts are finally available outside of your tool, just to know if the material contains holes, shrinkage or hot spots. If you rush to make the casting model and mold, you will surely face customer dissatisfaction, and worse, you will have to go back to designing the casting model and rebuild the casting mold, and hope that in the end the piece is free of defects. And since the test period in the foundry development program is underestimated, it is essential that the design of the mold gutters be strong against process changes before reaching the test stage.
Simulation allows virtual testing at an early stage of development. Accurate prediction and quantification of defects and process design are essential for "mold model design" during production testing.
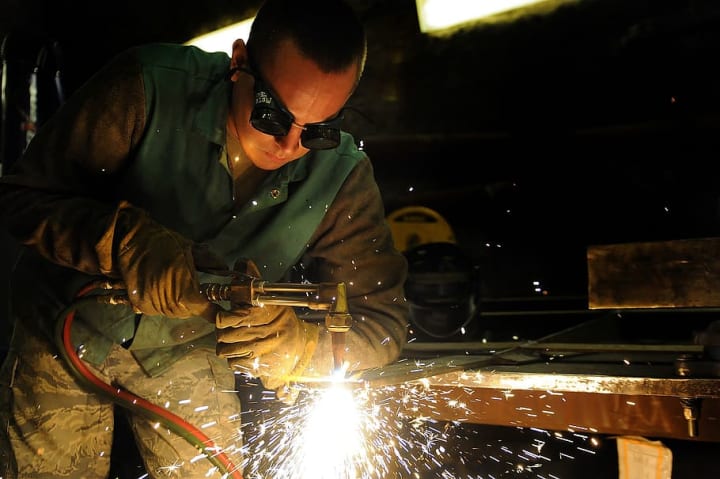
Two proposed software for casting simulation
With ESI ProCAST you can load your parts every time - this will prevent you from delivering scrap parts. For decades, customers have relied on ProCAST as their primary tool for casting principles - filling, solidification and porosity prediction. With its finite element technology, it also anticipates complex issues such as deformations and residual stresses, and comprehensively covers most casting alloys and most casting processes such as sand casting, casting molds, modeling. Eliminates precision casting and casting and the various types associated with these processes.
Another trusted and widely used software in the field of simulation of casting model making and then simulation of casting process that can be used with ease, software FLOW-3D CAST.
Further Details
Casting is one of the oldest processes in the production of metal parts. The variety of casting methods and the large number of variables in the process have led to the optimization of this process requires the use of software systems. Therefore, in this case, the costs of trial and error can be greatly reduced.
Among the commercial software in the field of casting, Proxt software is an accurate and reliable software, which will be reviewed in this training course.
ProCast software, which is the result of more than 30 years of constructive relationship with the casting industry, is able to perform various analyzes such as thermal, fluid, stress, microstructure and so on.
Miscellaneous Description
Industrial molds that are used for production have different types according to the production method of the part, which also differs according to the final part and the characteristics that are expected from that part. In general, the molds can be It was divided into four categories: 1- Casting molds 2- Plastic injection molds 3- Glass and crystal molds 4- Sambeh and matrix molds, each of which is divided into sub-sets according to the type of part. To be. However, considering that the main subject of this article is the study of two methods of making casting molds and the method of centralized and decentralized structure, we focus the main topic on the construction of casting molds so that we can go into more details of this discussion.
Today, due to technological advances in both the machine tool sector (especially the import of CNC machines) and in the software sector of the modeling industry, both in terms of reducing manufacturing time and the ability to build models with complex forms, significant progress has been made. He has seen it himself. This process is divided into two parts: design and construction. In the design department, the design engineer, according to his knowledge and experience, designs the execution, shape and also the gate system of the model using software such as CATIA, SOLID WORK, MECHANICAL and creates a three-dimensional model, which is a three-dimensional model. The machining base is placed by CNC machine, then after completing the machining operation, the model assembly process is performed.
The model making process is divided into two parts: the first part is the model design stage and the second part includes machining operations and assembling the model components. The three-dimensional model of the part is made using one of the CATIA, MECHANICAL or SOLID WORK software in the computer, after which the components of the model are separated and designed. After the design stage, it is the turn of the production stage, where the model components on wood are machined by CNC milling machine. The operator machining load with POWERMILL software executes the machining program on the 3D model given to him by the designer in the computer, then this program is given to the CNC machine and automatically runs on the wood, then these components are cast They are sent to make a piece of metal from it, then these components are tensioned to prevent them from deforming and warping after machining. After machining on the metal parts of the model, these components are assembled by the mold assembler, and finally the casting model is ready to use and produce the part.
About the Creator
PGM
I do Casting , and I love Investment Casting Technology.
Comments
There are no comments for this story
Be the first to respond and start the conversation.