5 Cost Reducing Benefits Of Volume Injection Molding
Molten can become so many useful items, read on
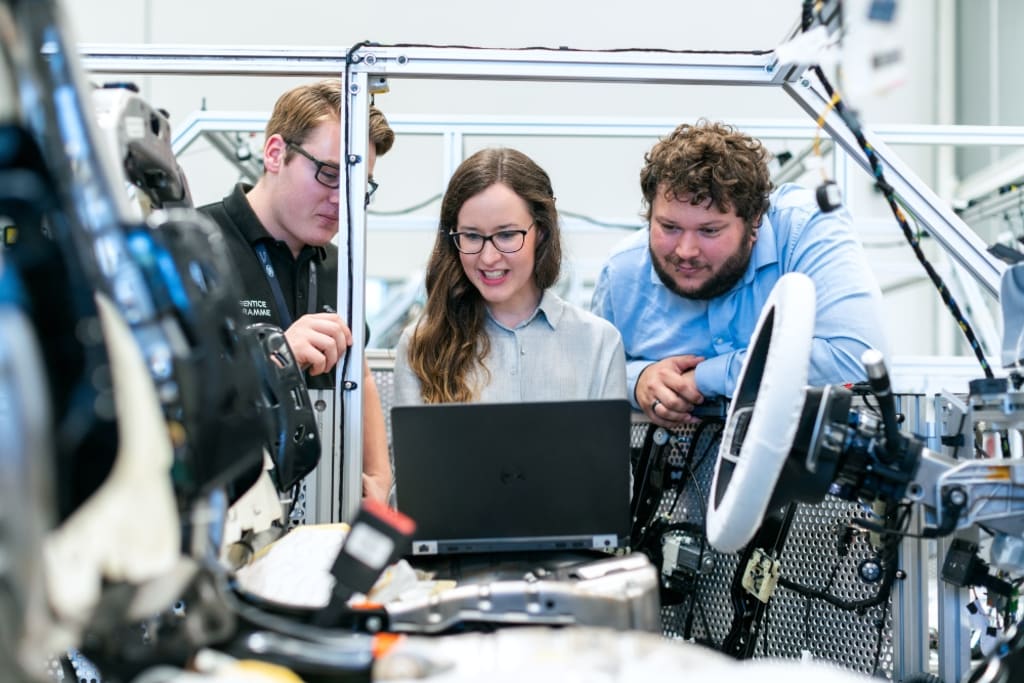
Injection Molding is a manufacturing process that entails injecting molten material into a cast or mold to produce parts. Molten material for the needed part is fed into a mold cavity, where it cools down and hardens to the configuration of the cavity. Injection molding can be done to various materials, such as metal, glass, elastomers, etc. This article presents the cost-reducing benefits of volume injection molding.
Cost
Low volume injection molding has a broad part production quantity. Contrary to popular belief, higher volumes of production do not necessarily reduce the overall cost per part. When introducing a new product into the market, it is advisable to produce a few parts first to see how they will do in the market. Otherwise, you may end up with lots of deadstock, all of which is a loss for your business. This is where Injection molding for a few parts becomes more cost-effective than high volume injection molding.
Inventory Management
One of the most significant pitfalls in manufacturing is the overproduction of parts, leading to excess inventory. Excess inventory can be costly to a business in terms of lost productivity, storage space, and extreme events, the need to dispose of the product. To avoid overproduction of parts, you should employ a production method that will produce fewer parts.
For high efficiency, you should analyze your company’s sales goals and delivery commitments to see whether the volume injection method for a few parts will solve your problem of overstocking. You can consult several companies for your low-volume molding needs to ensure you do not overstock. There are several engineering companies that you can consult with that offer post molding services.
Quick marketing time
In this technological era that comes with the constant demand to innovate or modify existing products in the market, the release time of your product can be your downfall or selling point. High-volume injection molding requires more time to produce parts; hence, you might be late in product release than your competitors. Production of a few final production parts that will allow for steady sales to be made without creating an unsustainable number of pieces in inventory will ensure that you stay ahead of your competitors and have successful deals.
Bridging Tool
When a product has been approved and performs well in the market, the common idea is to move from small-scale production to large-scale production. The move to large-scale production entails adopting high-volume injection molding to produce more parts. According to research, high volume injection molding takes two times longer than low volume molding. Due to this discrepancy, the chances of a company experiencing a lack of stock while switching to large-scale production are high.
This is where bridging is employed. While waiting for the new large-scale production parts to arrive, you can keep producing a few products using low-volume molding to ensure that you do not miss out on profits due to a lack of products for sale. Again, when you prove to your clients that you are not consistent, they are likely to move to more stable manufacturers.
Mold Cost
For High volume injection molding, steel is used to make the mold. But, this is not the case when producing less than 100,000 parts. When producing fewer parts, the molds are usually cut from a high-quality grade of aluminum. The difference in mold materials causes a difference in production charges depending on which mold material has been used. Steel is more expensive as compared to aluminum.
This, therefore, makes low volume molding a more cost-effective option for parts production for a company that deals with slow-selling parts to avoid overstocking. Low volume molding can also be a better option for companies running on a strict part production budget. Before deciding whether to go with the low or high-volume molding option, you need to think and rethink each option’s pros and cons. Otherwise, making a wrong call will make your venture unstable.
Last Words
Before starting production of any part, you should critically analyze all factors to ensure that whichever injection molding process you choose to employ will work well for you. Before selecting an injection molding process, you must learn all the injection molding factors worth considering.
About the Creator
Stephanie Snyder
Stephanie Caroline Snyder graduated from The University of Florida in 2018; she majored in Communications with a minor in mass media. Currently, she is an Author, a Freelance Internet Writer, and a Blogger.
Comments
There are no comments for this story
Be the first to respond and start the conversation.