Mastering Lean Manufacturing: Top 8 Tips & Trics to Automate Processes With Low Costs Tools
Master lean manufacturing with our top 8 tips and tricks. Automate your production processes using low-cost tools. Ideal for businesses aiming to implement lean principles without breaking the bank.
Mastering lean principles is imperative for sustained success. Lean manufacturing emphasizes efficiency, waste reduction, and continuous improvement to optimize processes and deliver value to customers. In this comprehensive guide, we'll explore ten actionable tips and tricks to automate manufacturing processes efficiently while keeping costs low.
Table of Contents
- Understanding Lean Manufacturing
- Importance of Warehouse Management in Lean Manufacturing
- Tips & Trics to Automate Processes
- The Role of WMS and WMS Add-ons in Automation
- Integrating ERP Systems for Seamless Operations
- Cost Reduction Strategies in Lean Manufacturing
- Conclusion
Understanding Lean Manufacturing
Before diving into the tips and tricks, it's crucial to have a solid understanding of lean manufacturing principles. Lean manufacturing is a strategic approach to manufacturing that emphasizes the elimination of waste, optimization of processes, and continuous improvement to enhance efficiency and productivity. At its core, lean manufacturing aims to deliver maximum value to customers while minimizing resources, time, and effort expended in the production process.
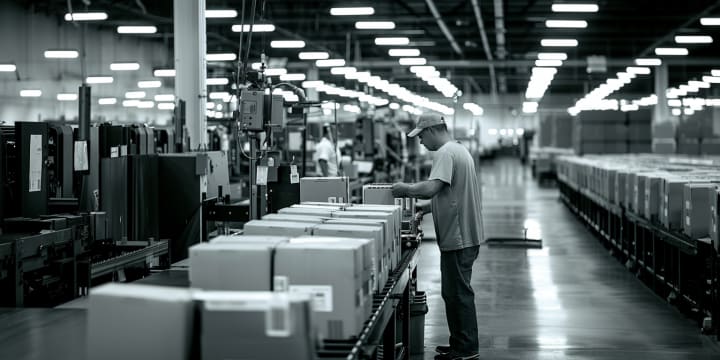
Importance of Warehouse Management in Lean Manufacturing
Warehouse management plays a pivotal role in the success of lean manufacturing by ensuring efficient handling, storage, and movement of materials throughout the production process. In a lean manufacturing environment, where the focus is on eliminating waste and maximizing value, effective warehouse management is essential for achieving operational excellence and delivering superior customer satisfaction.
- Optimized Inventory Levels: One of the core principles of lean manufacturing is minimizing inventory to reduce costs and increase efficiency. Warehouse management ensures that inventory levels are optimized, with just enough stock on hand to meet production demands without excess. By maintaining lean inventory levels, businesses can minimize carrying costs, reduce the risk of overstocking or stockouts, and improve cash flow.
- Streamlined Operations: Efficient warehouse management streamlines operations by ensuring that materials are readily available when needed. Through proper organization, layout design, and inventory management techniques, warehouses can minimize the time and effort required to locate, retrieve, and transport materials to the production line. This reduces lead times, eliminates unnecessary delays, and improves overall productivity.
- Accurate Order Fulfillment: In lean manufacturing, accuracy is paramount. Warehouse management systems (WMS) help ensure accurate order fulfillment by tracking inventory in real-time and providing visibility into stock levels, locations, and status. By leveraging WMS technologies such as barcode scanning and RFID tagging, warehouses can minimize picking errors, reduce order processing times, and enhance customer satisfaction.
- Optimized Inventory Levels: Proper warehouse management involves optimizing space utilization to maximize storage capacity and minimize wasted space. Through efficient layout design, shelving systems, and storage solutions, warehouses can accommodate more inventory within the same footprint, reducing the need for additional storage facilities and associated costs. This also facilitates easier access to materials, improving operational efficiency and workflow.
- Inventory Accuracy and Control: Lean manufacturing relies on accurate inventory data to support decision-making and planning processes. Warehouse management ensures inventory accuracy through regular cycle counts, stock audits, and reconciliation processes. By maintaining accurate inventory records, businesses can avoid costly errors such as stockouts, overages, or obsolete inventory, leading to improved inventory control and financial performance.
Enhanced Customer Service: Ultimately, effective warehouse management contributes to enhanced customer service and satisfaction. By ensuring timely order fulfillment, accurate inventory availability, and reliable delivery, warehouses play a critical role in meeting customer expectations and building long-term relationships. Satisfied customers are more likely to return for repeat business and recommend the company to others, driving growth and profitability.
Warehouse Management in Lean Manufacturing. Learn more >>
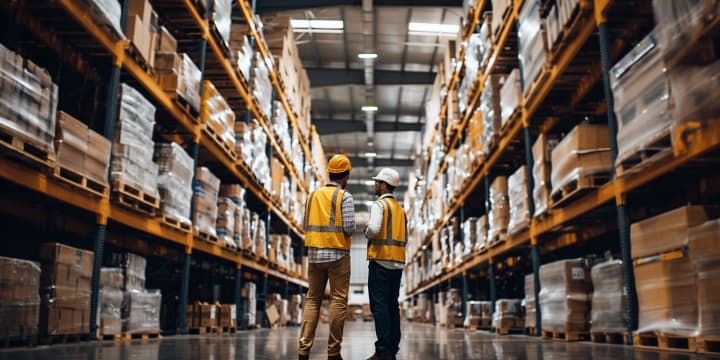
Tips & Trics to Automate Processes
1. Standardize Processes for Efficiency
By establishing clear, standardized procedures for every task, businesses can minimize variation, reduce errors, and enhance efficiency. Implementing robust warehouse management systems (WMS) and enterprise resource planning (ERP) systems streamlines operations, providing a solid foundation for process standardization. ERP systems like SAP and Oracle offer comprehensive solutions for process optimization and data management, enabling businesses to achieve greater visibility and control over their operations.
2. Embrace Just-In-Time (JIT) Inventory Management
By minimizing inventory levels and replenishing supplies only when needed, businesses can reduce storage costs, eliminate waste, and improve cash flow. Leveraging WMS add-ons and ERP systems with advanced inventory management capabilities enhances visibility and control over inventory levels, enabling businesses to optimize their JIT processes effectively.
3. Leverage Warehouse Digitalization for Efficiency Gains
By embracing digital technologies such as automation, robotics, and IoT devices, businesses can streamline warehouse operations, reduce errors, and improve overall efficiency. Implementing warehouse management systems (WMS) with digitalization capabilities enhances visibility and transparency across the supply chain, enabling real-time monitoring and decision-making.
4. Invest in Employee Training for Continuous Improvement
Investing in employee training and development is essential for fostering a culture of continuous improvement in lean manufacturing. Providing comprehensive training programs equips employees with the skills and knowledge needed to excel in their roles and contribute to process optimization. ERP systems like MS Dynamics and Odoo offer built-in training modules and resources, empowering employees to leverage technology effectively for process improvement and innovation.
5. Optimize Equipment Utilization for Cost Savings
Conducting regular maintenance and utilizing predictive maintenance tools help minimize downtime and prevent costly breakdowns. ERP systems integrated with equipment monitoring modules provide real-time insights into equipment performance and health, enabling proactive maintenance and optimization.
6. Implement Quality Assurance Measures for Error Reduction
Quality assurance is paramount in lean manufacturing to ensure product quality and customer satisfaction. Implementing robust quality control processes and conducting regular inspections help identify and mitigate errors early in the production process. ERP systems like Sage and Infor offer comprehensive quality management modules, enabling businesses to establish and enforce quality standards effectively throughout the manufacturing process.
7. Foster Collaboration and Communication Across Departments
Effective communication and collaboration are essential for streamlining processes and improving efficiency in lean manufacturing. Breaking down silos between departments and fostering a culture of collaboration enables cross-functional teams to work together towards common goals. Utilizing collaboration tools integrated into ERP systems, such as project management and communication platforms, facilitates seamless communication and information sharing across the organization.
8. Continuously Evaluate and Improve Processes
Regularly reviewing processes, gathering feedback from employees, and analyzing performance metrics help identify areas for optimization and refinement. Leveraging data analytics tools integrated into ERP systems allows businesses to gain valuable insights into their operations, enabling data-driven decision-making and continuous improvement initiatives.
The Role of WMS and WMS Add-ons in Automation
Warehouse Management Systems (WMS) and their add-ons play a pivotal role in automating various aspects of warehouse operations, driving efficiency, accuracy, and cost-effectiveness.
WMS in Automation
WMS is the backbone of warehouse automation, serving as the central hub for managing and controlling all warehouse activities. It encompasses a range of functionalities, including inventory management, order processing, picking and packing, shipping, and receiving.
One of the primary functions of WMS in automation is inventory management. By leveraging real-time data capture technologies such as barcode scanning and RFID, WMS provides accurate visibility into inventory levels and locations throughout the warehouse. This visibility enables businesses to optimize stock levels, reduce excess inventory, and minimize stockouts, thereby improving overall inventory efficiency.
WMS also plays a crucial role in order processing and fulfillment. Through automation algorithms and intelligent routing, WMS optimizes order picking routes, minimizes travel time, and maximizes picking accuracy. This automation reduces manual errors, increases order throughput, and enhances customer satisfaction by ensuring timely and accurate order fulfillment.
In addition to inventory and order management, WMS facilitates seamless inbound and outbound logistics operations. It automates receiving processes by capturing and processing inbound shipments efficiently, enabling quick put-away and storage allocation. Similarly, WMS automates outbound processes such as packing, labeling, and shipping, ensuring accurate and timely order delivery to customers.
WMS Add-ons in Automation
In addition to core WMS functionalities, businesses can further enhance warehouse automation through the integration of WMS add-ons. These add-ons extend the capabilities of WMS and address specific operational requirements, thereby maximizing automation benefits.
One common WMS add-on is slotting optimization software, which optimizes warehouse layout and storage configurations based on inventory characteristics, demand patterns, and order profiles. By dynamically reorganizing storage locations and slotting high-demand items closer to picking areas, slotting optimization software reduces travel time, minimizes congestion, and improves picking efficiency.
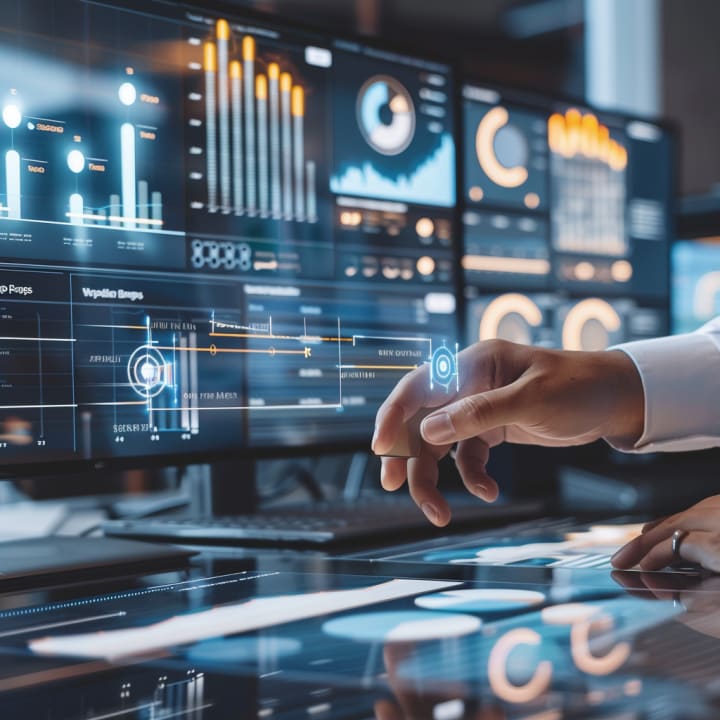
Integrating ERP Systems for Seamless Operations
Integrating Enterprise Resource Planning (ERP) systems is a critical aspect of achieving seamless operations in lean manufacturing. ERP systems serve as the backbone of the organization, centralizing data and facilitating communication between different departments and functions. When integrated with warehouse management systems (WMS), ERP systems enable a unified approach to managing resources, processes, and information across the entire manufacturing lifecycle.
One of the primary benefits of integrating ERP systems in lean manufacturing is improved data accuracy and consistency. By centralizing information related to inventory levels, production schedules, and customer orders, ERP systems ensure that all stakeholders have access to real-time, up-to-date data. This eliminates discrepancies and reduces the risk of errors, enabling better decision-making and resource allocation.
In addition to improving operational efficiency, integrating ERP systems in lean manufacturing can also drive cost savings. By eliminating redundant systems and streamlining processes, ERP integration reduces overhead costs and improves resource utilization. Furthermore, by providing greater visibility into costs and performance, ERP systems enable better cost management and budgeting decisions.
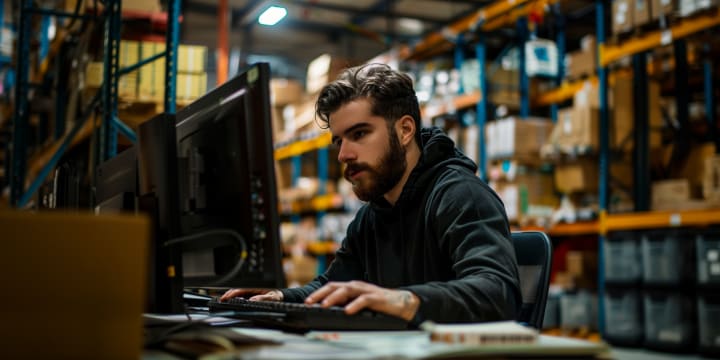
Overall, integrating ERP systems is essential for achieving seamless operations in lean manufacturing. By centralizing data, enhancing visibility, streamlining workflows, and facilitating collaboration, ERP integration enables organizations to unlock new levels of efficiency, productivity, and competitiveness in today's dynamic business environment.
Cost Reduction Strategies in Lean Manufacturing
Cost reduction is a fundamental objective in lean manufacturing, aimed at optimizing expenses while maintaining or improving product quality and customer satisfaction. Businesses employ various strategies to identify and eliminate waste across their operations, ultimately enhancing profitability:
- Process Optimization: Lean manufacturing emphasizes streamlining processes to eliminate non-value-added activities and minimize waste. By conducting thorough process analysis and reengineering, businesses can identify inefficiencies and bottlenecks, leading to significant cost savings. Process optimization may involve redesigning workflows, standardizing procedures, and adopting lean tools and techniques such as value stream mapping and 5S methodology.
- Supplier Collaboration: Collaborating closely with suppliers is essential for reducing costs in lean manufacturing. Businesses can negotiate favorable terms, bulk discounts, and payment schedules with suppliers to lower procurement costs. Additionally, establishing long-term partnerships and fostering open communication can lead to better pricing, quality improvements, and innovation.
- Inventory Management: Effective inventory management is critical for minimizing carrying costs and reducing waste in lean manufacturing. By implementing just-in-time (JIT) inventory systems, businesses can maintain optimal inventory levels and avoid overstocking. Furthermore, adopting inventory optimization techniques such as ABC analysis and demand forecasting can help prevent stockouts and excess inventory, leading to cost savings and improved cash flow.
- Lean Production Techniques: Lean manufacturing employs various production techniques to eliminate waste and improve efficiency. Techniques such as single-piece flow, pull production, and kanban systems help reduce lead times, inventory levels, and production costs. By focusing on value-added activities and minimizing non-value-added tasks, businesses can achieve higher productivity and lower production costs.
- Quality Improvement: Quality issues can result in costly rework, scrap, and warranty claims in manufacturing processes. Lean manufacturing emphasizes building quality into processes from the outset, rather than inspecting defects out. By implementing quality control measures, error-proofing techniques, and continuous improvement initiatives, businesses can enhance product quality while reducing defects and associated costs.
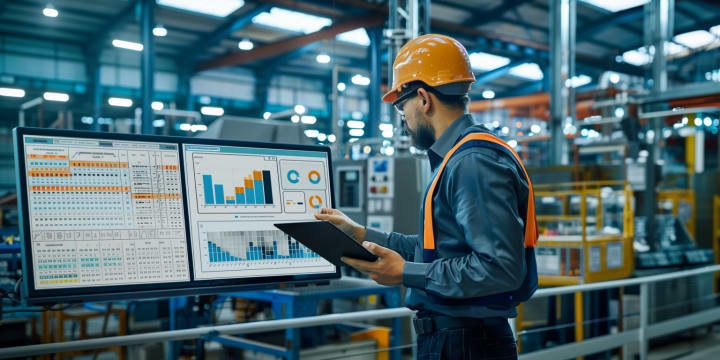
In summary, cost reduction strategies in lean manufacturing encompass a range of approaches aimed at optimizing processes, improving efficiency, and eliminating waste. By implementing these strategies systematically and engaging employees at all levels, businesses can achieve significant cost savings while enhancing overall performance and competitiveness.
Conclusion
In conclusion, effective implementation of lean manufacturing principles requires a comprehensive strategy that encompasses various aspects of operations, including warehouse management, inventory optimization, digitalization, cost reduction, and integration with ERP systems. This strategic approach not only enables organizations to meet customer demands more effectively but also positions them for long-term success and growth in today's competitive marketplace.
Comments
There are no comments for this story
Be the first to respond and start the conversation.